Many manufacturers ask whether they should focus on Demand Flow Technology (DFT) or Lean manufacturing. If you’ve read our previous article, DFT vs. Lean – A Guide for Manufacturing Leaders, you know that while DFT and Lean share the goal of flow, their methods differ.
- DFT creates the foundation and framework — a demand-driven operating model designed for speed, flexibility, and efficiency.
- Lean provides the toolkit — continuous improvement methods that sustain, refine, and evolve the DFT system over time.
This post examines how DFT and Lean are not competing methodologies, but rather complementary disciplines. When used together, they create a powerful manufacturing operating model that delivers both rapid operational transformation and long-term continuous improvement.
DFT Creates the Flow – Lean Drives Improvement
DFT: The Operational Backbone
DFT is the structural framework and transformational business strategy needed to shift traditional manufacturing from push-based, forecast-driven production to true demand-driven manufacturing. Its design principles include:
- Flow Path Design – Defining the most efficient material and process flow aligned to demand.
- Process Balancing – Ensuring each process step is synchronized to customer demand
- Mixed-Model Production – Flexibly building multiple SKUs without batching or large setups. In essence, build any product on any day to customer demand
- Visual Scheduling – Using real-time demand signals to drive production rather than relying on traditional push-based schedules.
This is not a set of incremental improvements—DFT is a fundamental redesign of operations that enables step-change, affecting layouts, processes, planning, and execution to create flow that minimizes lead time, reduces WIP, and maximizes flexibility.
Lean: The Accelerator for DFT Deployment
Once the DFT design is in place, Lean tools become critical enablers. They stabilize, support, and accelerate the launch of the demand-driven model.
Lean Tool | How It Supports DFT |
5S | Organizes workstations, eliminates clutter, improves visibility, enabling flow stability. |
SMED (Quick Changeover) | Reduces setup times — essential for mixed-model production in a DFT environment. |
Kaizen Events | Drives rapid, focused problem-solving to eliminate barriers to flow. |
Standard Work | Ensures process consistency across operators and shifts, stabilizing flow. |
Error Proofing (Poka-Yoke) | Prevents defects that would disrupt the smooth operation of demand-driven flow. |
Visual Management | Provides feedback aligned with demand signals, complementing DFT’s visual scheduling. |
These tools don’t replace DFT — they enable and strengthen it.
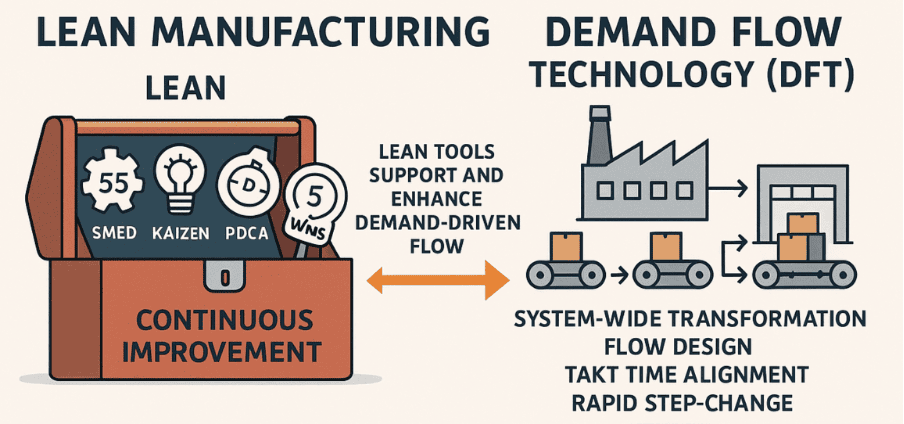
Lean Tools Are Embedded Within the Demand-Driven Operating System
During The DFT Implementation
Lean tools are not something you apply after DFT—they are built into how DFT gets deployed:
- 5S is often conducted alongside the physical layout changes driven by flow path design and line balancing.
- SMED is critical for enabling DFT’s mixed-model flexibility and capacity improvements.
- Kaizen becomes a standard activity during DFT implementation, driving quick problem resolution, fine-tuning processes, and optimizing layouts.
- Standard Work and Visual Management are essential for stabilizing the new flow lines.
After DFT Deployment
Implementing Demand Flow Technology is a transformative milestone for any organization. However, the journey doesn’t end once DFT is up and running. In fact, it marks the beginning of a new phase where continuous improvement becomes the primary focus. Here, Lean principles take center stage, acting as the engine that powers ongoing enhancements to your operations.
With DFT operational, the challenge shifts from building the system to refining it. Lean methodologies are now essential for:
- Process Optimization: Eliminating minor wastes that can accumulate over time.
- Layout Refinements: Adjusting physical setups as demand patterns evolve.
- Standard Work Updates: Modifying procedures as product mix or volume changes.
This continuous dedication to improvement keeps your DFT environment agile, efficient, fully aligned and responsive to evolving market demands. At this stage, the principles of Lean become even more essential, driving sustained excellence and adaptability.
Key Lean Practices Post-DFT:
- Ongoing SMED & Flexibility Gains. As product mixes expand, Single-Minute Exchange of Dies (SMED) and other setup reduction techniques remain crucial. They help preserve flow efficiency by minimizing downtime during changeovers.
- Kaizen for Process Refinement. Regular kaizen events drive the elimination of new wastes, address minor inefficiencies, and solve emerging problems before they escalate.
- Error Proofing & Quality Control. With flow established, maintaining zero-defect execution is vital. Error-proofing (poka-yoke) and robust quality controls become even more critical to prevent disruptions.
- Standard Work Evolution. Standard work is a living document. As products and processes change, standard work must be regularly updated to ensure consistency with the current state.
- Capacity & Resource Adjustments. As flow matures and improvements are implemented, layout adjustments or even process redesigns may be required to maintain optimal performance.
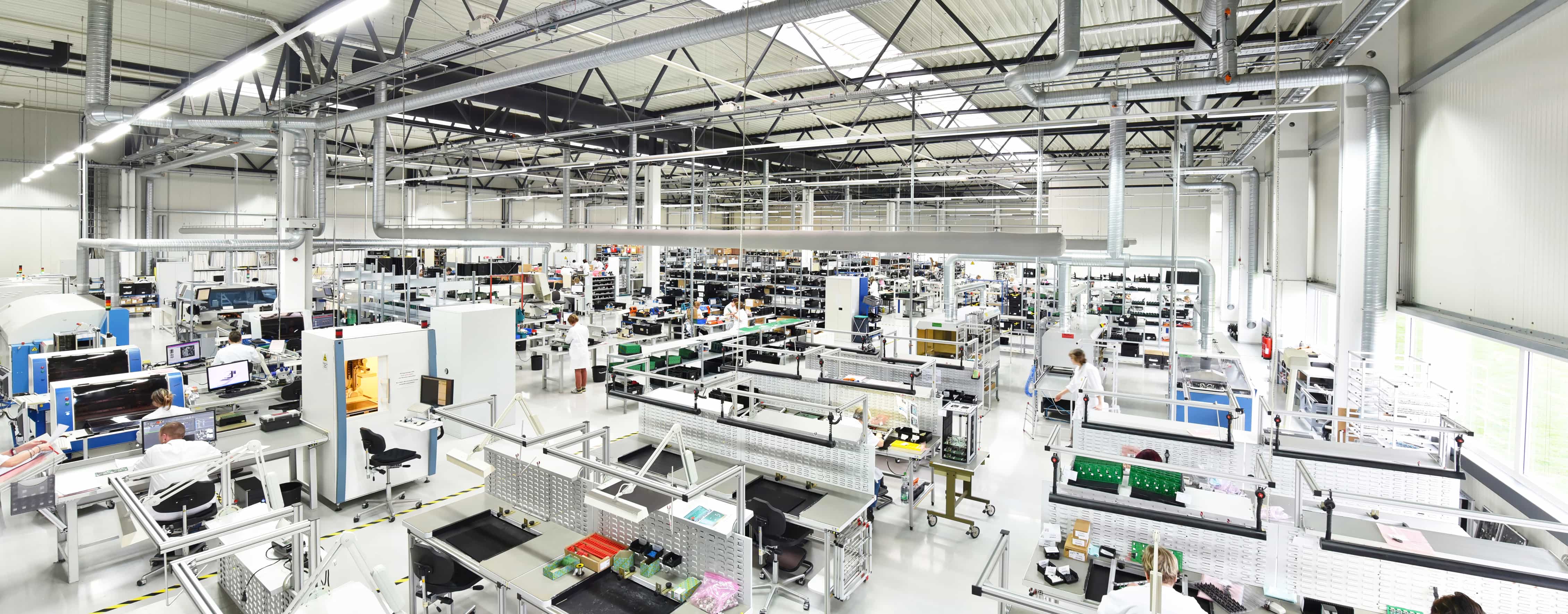
The Lifecycle of the Demand-Driven Operating System
DFT lays the essential foundation, but it is Lean that keeps the engine running smoothly. By embedding Lean practices into daily operations, organizations ensure their DFT systems not only sustain performance but also continuously improve—delivering lasting value and a strong competitive advantage.
However, the DFT environment naturally evolves. Business strategies shift, markets change, product mixes vary, and customer demands fluctuate. In this dynamic landscape, DFT serves as a platform for ongoing adaptation. As these changes occur, the original DFT design must be reassessed and rebalanced—often requiring a redesign to maintain optimal flow.
When to Redesign Your DFT Flow Line
You should consider a comprehensive redesign of your DFT system when significant changes in key business drivers or operational realities arise that cannot be addressed by minor adjustments. Key indicators include:
- Substantial shifts in demand or product mix: Significant changes in customer requirements, order volumes, or product types may render the existing flow suboptimal. Regular reviews (every 6–12 months) help catch these shifts early.
- Major process, equipment, or technology changes: Upgrades, new machinery, or process modifications can disrupt the balance and synchronization of your original DFT design.
- Introduction of new products or product families: Adding or retiring major products often requires re-evaluating flow, resource allocation, and line balancing.
- Persistent performance gaps: Ongoing issues with throughput, lead times, inventory levels, or quality that cannot be resolved through incremental improvements may signal the need for a full redesign.
- Changes in material supply or supplier base: New suppliers, materials, or replenishment strategies can impact how the line should be structured and supplied.
- Organizational growth or restructuring: Expansion, mergers, or significant workforce changes can alter capacity requirements and operational flow.
A systematic review process—ideally tied to your Sales & Operations Planning (S&OP) cycle—should feed real-world data back into your DFT model. When this review reveals that the current design no longer aligns with business needs, it’s time for a comprehensive redesign rather than incremental tweaks.
Organizations that treat DFT as a static solution risk slipping back into inefficiency and losing their competitive edge. By regularly refreshing flow design through DFT principles, manufacturers can remain agile and competitive—quickly adapting to new challenges and seizing emerging opportunities in the market.
Conclusion: A Symbiotic Relationship
The relationship between Demand Flow Technology (DFT) and Lean is not about choosing one over the other—it’s about harnessing the strengths of both to create a powerful, adaptive manufacturing system.
- DFT establishes the demand-driven operating system.
- Lean acts as the continuous improvement engine, ensuring the system runs at peak performance
Together, DFT and Lean create a manufacturing model that delivers:
- Faster lead times
- Lower inventory levels
- Higher productivity
- Increased capacity
- Greater flexibility and responsiveness
By integrating DFT and Lean, organizations position themselves to thrive in a dynamic market—achieving operational excellence and sustaining a true competitive advantage.
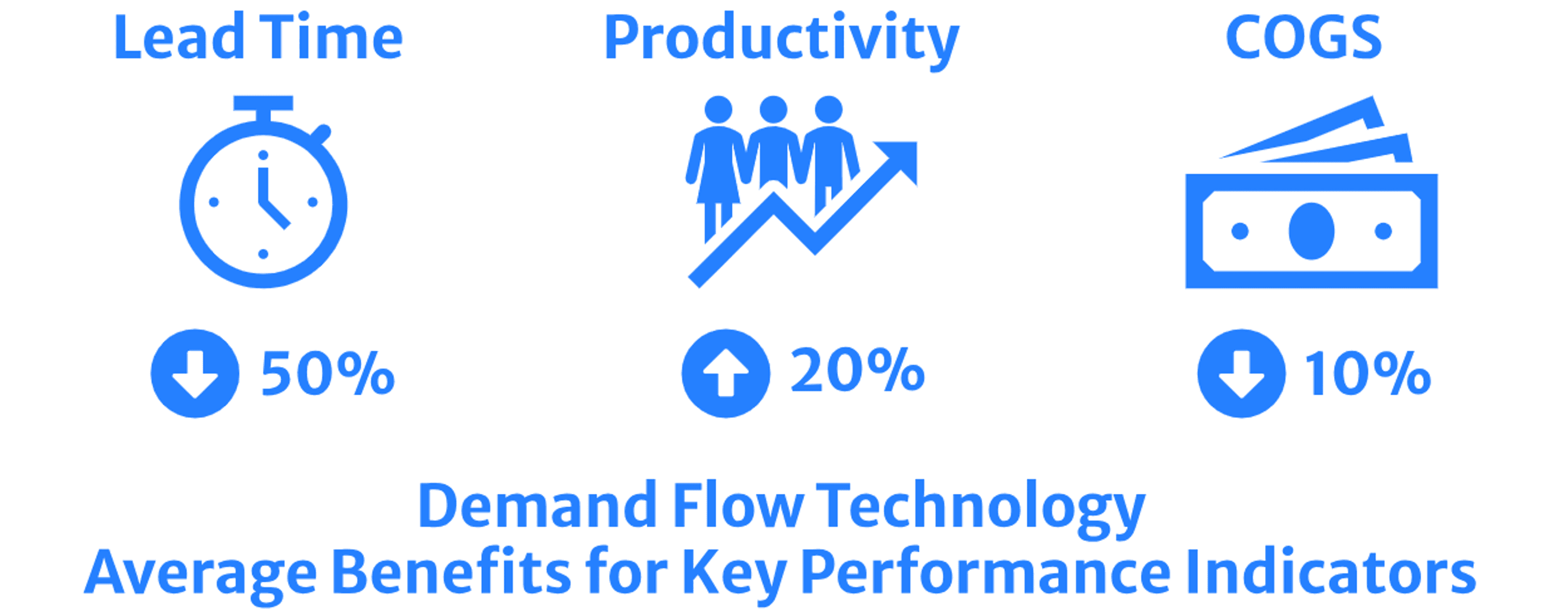
Summary Takeaways
- DFT establishes demand-driven flow: DFT creates the foundation and framework for a responsive and efficient operating system.
- Lean tools accelerate DFT deployment: Lean principles and methods streamline implementation and maximize early results.
- Continuous improvement keeps DFT relevant: Ongoing Lean-driven improvements ensure the DFT design adapts as demand and market conditions evolve.
- Together, DFT and Lean drive operational excellence: DFT and Lean, combined strengths deliver lasting value, agility, and a true competitive edge.
Demand Driven Supply Chain Solutions
High Impact Coaching & Strategies helps manufacturers worldwide boost productivity, cut costs, and increase agility by aligning manufacturing and supply chain with real customer demand. Using Demand Flow Technology and Demand Driven Supply Chains strategies, we enable faster lead times, lower costs, and improved customer satisfaction—generating sustainable bottom-line benefits and creating a sustainable competitive advantage.
To learn more, contact us at info@highimpactcs.com or send a message via our contact page.
Manufacturing & Supply Chain Information
Previous Insights from High Impact Coaching & Strategies:
- DFT vs Lean: A Guide for Manufacturing Leaders
- What is Demand Flow Technology
- The Tools of Demand Flow Technology
- How Demand Flow Technology Impacts The Health of Your Business (3-part series)
- Cash Flow Generation is a Priority (2-part series)
- Review of a Recent Demand Flow Technology Implementation
- An Introduction to Sales and Operations Planning S&OP (2-part series)
- What is Supply Chain Management?
- Supply Chain Planning & Engineering
Overview of High Impacts’ Demand Driven strategies that will transform your factories and supply chain network:
LinkedIn Information:
Newsletter Sign-Up
Keep up-to-date on with what’s happening in our Demand Driven World. Get information manufacturing and supply chain topics as well as news on client achievements, up and coming training events and other interesting stuff!
Talk to us today to learn more about how we can help your organization become Demand Driven through the adoption of our Demand Driven methodologies, Demand Flow Technology and Demand Driven Supply Chains.