High Impact’s Experience
High Impact Coaching & Strategies has developed a strong reputation from working with our clients based in Asia, Europe and the Americas achieving swift, sustainable and scalable bottom-line benefits. Our team has extensive knowledge of manufacturing and are expert in the creation of world-class Demand Driven Manufacturing and Supply Chains.
We are the market leaders in establishing flow within manufacturing organizations and the only company that leverages Demand Flow Technology within the factory and Demand Driven MRP across the entire end-to-end supply chain to achieve outstanding benefits for our clients. Our experience covering a wide and diverse range of manufacturing industries has enabled us to cater for almost any possible obstacle hindering the growth of the companies we work with.
Our systematic and assertive approach enables all of our clients to develop a competitive edge through advanced manufacturing and supply chain methodologies that deliver exceptional and scalable benefits.
Industrial Sectors
Over the past two decades we have created an integrated approach in the delivery of our projects that links our stakeholders from shop floor to the board in over dozens of industry sub-sectors that include:
- Aerospace
- Aerospace equipment & electronics
- Automotive
- Commercial Audio Equipment
- Consumer Goods
- Food Products
- Gas Compressors
- Heavy Manufacturing
- HVAC
- Industrial Electronics
- Industrial Engineering
- Medical Devices
- Mining Equipment
- Pharmaceutical
- Safety Devices
- Semiconductor Equipment
- SMT Production
- White Goods
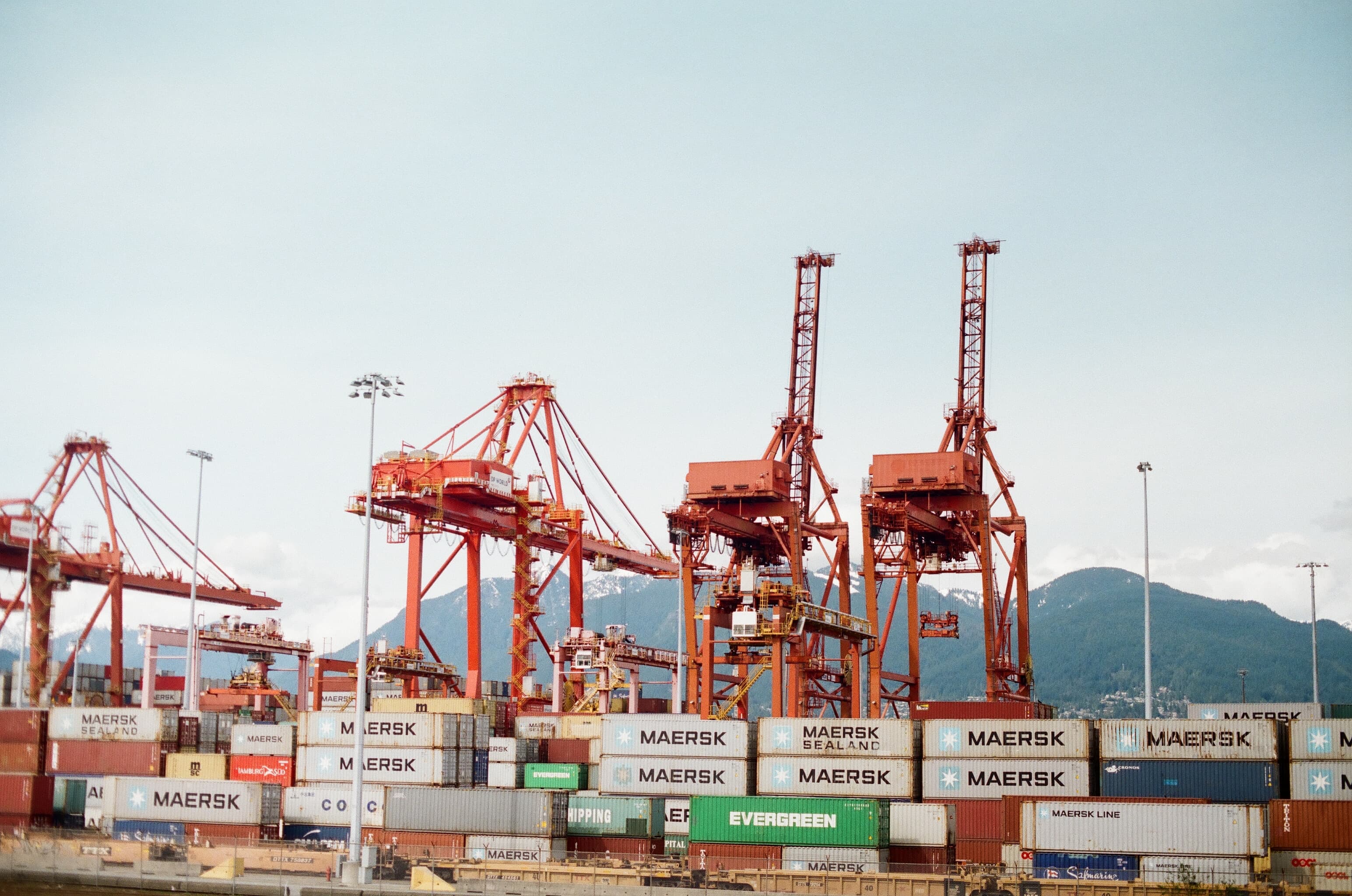
Industrial Sectors
Over the past two decades we have created an integrated approach in the delivery of our projects that links our stakeholders from shop floor to the board in over dozens of industry sub-sectors that include:
- Aerospace
- Aerospace equipment & electronics
- Automotive
- Commercial Audio Equipment
- Consumer Goods
- Food Products
- Gas Compressors
- Heavy Manufacturing
- HVAC
- Industrial Electronics
- Industrial Engineering
- Medical Devices
- Mining Equipment
- Pharmaceutical
- Safety Devices
- Semiconductor Equipment
- SMT Production
- White Goods
Manufacturing and Supply Chain Issues
Over the years we have assisted our clients to overcome a wide variety of problems and achieve the business improvements and sustainable bottom-line benefits they need to be a competitive force in the market. Sometimes companies believe their problems are unique to them, however the root causes are typically common to issues that we know very very well. The most common manufacturing and the supply chain issues that we have resolved can be summarized as:
- Consistency of manufacturing methods across global facilities
- Consistency in product build
- Excessive lead times
- Excessive WIP levels
- Fragmented fulfilment system
- Lack of manufacturing and supply chain capacity
- Operational Response Consistency
- Poor cash flow
- Poor levels of customer service
- Poor supplier response
- Resource utilization
- Value chain expenses
- Working capital efficiency
Demand Driven Business Improvement Solutions
Manufacturing and supply chain operations are challenging. We hear from C-Level executives all of the time that business improvement projects fail to deliver bottom-line benefits for the business. Our array of business improvement solutions solve this problem. We help our clients to leverage the skills of their organization along with our knowledge and expertize of demand driven manufacture and supply chain methodologies to deliver rapid and sustainable benefits.
Through a deep understanding of our client and their operations, our solutions enable organizations to align with the needs of the market and being responsive, agile and adaptive enough to cope when change occurs. Recent global solutions implemented by our team that have achieved real benefits include:
- Creation of a Demand Flow Technology factory (single site and across global factory footprint)
- Creation of planning families linked to operational capabilities
- Demand Driven Kanban design solutions
- Deployment of Finished Goods Inventory strategies to align with the needs of the market
- Excellence platform integrated to company’s Demand Driven supply initiative
- Factory response improvements leveraged to increase manufacturing capacity, reduce working capital and improve cash flow
- Global Supply Chain, Supplier Integration and Demand Flow Technology factory solutions
- Reliable and predictable Operational response
Manufacturing and Supply Chain Success
Our total commitment to our client and our flexible approach has enabled High Impact Coaching & Strategies to achieve a considerable track record for the successful delivery of a wide range of manufacturing and supply chain business improvement projects ensuring we position our clients at the forefront of their industry. With our solutions in place, our clients can stay ahead of the competition through sustainable and scaleable bottom-line benefits.
The work performed with our customers has facilitated faster response times and combatted demand volatility in the factory and throughout the supply chain enabling our clients to service their customers quicker, reduce inventory and costs. Significant bottom-line results have been achieved directly from the following list of tangible and real benefits:
Beverage Refrigeration
- 69% Productivity improvement
- $1.9 Million savings over 1st 12-months
- 14 :1 ROI with 3-month Payback
Commercial and Industrial Air-Conditioning
- 10% Productivity improvement
- 60% WIP improvement
- 46% Capacity improvement
Electronics
- 70% Lead time reduction
- 16% Capacity improvement
- 20% Headcount reduction redeployed to other lines
- 41% Productivity improvement due to reduced labor hours
- 23% Cost of Goods Sold (COGS) reduction
- 16:1 ROI with a 1-month payback
- Elimination of order backlog within 3-months, a feat never experienced before
Gas Detection Devices
- 83% Manufacturing lead time reduction
- 50% Customer lead time reduction
- 200% Manufacturing capacity increase without additional resources
- 45% Service center capacity increase with a 20% reduction in resources
Hydraulic Actuation Valve
- 98% Manufacturing lead time reduction
- 20% Productivity improvement
- 35% WIP improvement
- $1 million savings
Industrial Electronics
- 38% Manufacturing lead time reduction
- 25% WIP improvement
- 10% Space reduction
- Up to 60% reduction in supplier lead times
- $60 Million working capital reduction
- 12% Customer service improvement
Industrial Valve Manufacturer
- 80% Manufacturing lead time improvement
- 36% Capacity increase
- 25% Productivity improvement
- Elimination of works orders
- Elimination of past due orders within 6 months (the first time in 10 yrs.)
Medical Equipment
- 21% Manufacturing lead time reduction
- 17% Productivity improvement
- $1.7 Million savings
Oil Tanker Trailers
- 55% Manufacturing lead time reduction
- 47% Productivity improvement
- 66% Capacity improvement
Pharmaceuticals
- 47% Lead time reduction (from 92 days to 50 days)
- 55% QA Documentation processing lead time reduction
- 60% WIP improvement
- Global savings of over $650 million in working capital
Pharmaceutical Supplier
- 10% Lead time improvement
- 15% Productivity improvement
- 10% WIP improvement
- 20% Overtime reduction
- 90% Quality re-inspection reduction
Beverage Refrigeration
- 69% Productivity improvement
- $1.9 Million savings over 1st 12-months
- 14 :1 ROI with 3-month Payback
Commercial and Industrial Air-Conditioning
- 10% Productivity improvement
- 60% WIP improvement
- 46% Capacity improvement
Electronics
- 70% Lead time reduction
- 16% Capacity improvement
- 20% Headcount reduction redeployed to other lines
- 41% Productivity improvement due to reduced labor hours
- 23% Cost of Goods Sold (COGS) reduction
- 16:1 ROI with a 1-month payback
- Elimination of order backlog within 3-months, a feat never experienced before
Gas Detection Devices
- 83% Manufacturing lead time reduction
- 50% Customer lead time reduction
- 200% Manufacturing capacity increase without additional resources
- 45% Service center capacity increase with a 20% reduction in resources
Hydraulic Actuation Valve
- 98% Manufacturing lead time reduction
- 20% Productivity improvement
- 35% WIP improvement
- $1 million savings
Industrial Electronics
- 38% Manufacturing lead time reduction
- 25% WIP improvement
- 10% Space reduction
- Up to 60% reduction in supplier lead times
- $60 Million working capital reduction
- 12% Customer service improvement
Industrial Valve Manufacturer
- 80% Manufacturing lead time improvement
- 36% Capacity increase
- 25% Productivity improvement
- Elimination of works orders
- Elimination of past due orders within 6 months (the first time in 10 yrs.)
Medical Equipment
- 21% Manufacturing lead time reduction
- 17% Productivity improvement
- $1.7 Million savings
Oil Tanker Trailers
- 55% Manufacturing lead time reduction
- 47% Productivity improvement
- 66% Capacity improvement
Pharmaceuticals
- 47% Lead time reduction (from 92 days to 50 days)
- 55% QA Documentation processing lead time reduction
- 60% WIP improvement
- Global savings of over $650 million in working capital
Pharmaceutical Supplier
- 10% Lead time improvement
- 15% Productivity improvement
- 10% WIP improvement
- 20% Overtime reduction
- 90% Quality re-inspection reduction
Case Study
Advanced Energy Industries, Inc., is a high-tech manufacturer specializing in power conversion solutions utilized in thin-film plasma manufacturing and solar energy generation. This case study reviews the work that was completed in their facility located in Shenzhen China and the improvements that they have achieved.
Case Study
Advanced Energy Industries, Inc., is a high-tech manufacturer specializing in power conversion solutions utilized in thin-film plasma manufacturing and solar energy generation. This case study reviews the work that was completed in their facility located in Shenzhen China and the improvements that they have achieved.
With TheONE, your focus is on the overall Demand Flow Technology (DFT) design rather than on non-value added activities associated with spreadsheet manipulation. It provides a really great user-friendly step-by-step process to follow when designing your DFT flow line.
Our instructor, Sandy Goodwin, was extremely knowledgeable, patient, professional and had an excellent disposition. The course material was in-depth and thoroughly discussed.
Our product mix ranges from extreme high mix, low volume to low mix, medium volume. We selected Demand Flow Technology (DFT) as the foundation for Manufacturing and Supply Chain because of its flexibility in supporting the volatility of our product mix. It provides our teams with a common language for planning and staging material in the supply chain and within the factory. Our customers require agility and speed for delivery of quality products and our stakeholders require cash conservation with our inventory strategies. DFT is our platform to achieve these requirements.
It was a pleasure to be part of the class and I guarantee the materials I learnt will be part of my daily activities in production.
All knowledge was presented in an extremely attractive and easy to understand way. I’m so glad that I had the chance to participate.
Our consultant was extremely knowledgeable and presented the material in a way that was easy to understand but also challenged you to think through solutions. This of course was extremely beneficial and can be applied to every aspect of the business.
Thank you for providing a high level of quality training. I really enjoyed your presentation and willingness to take the time and answer all the questions that were presented.
This week, I finished a fantastic DFT training led by Sandy Goodwin. Grateful for the top-notch instruction and thoroughly enjoyed the class. Appreciate the opportunity to enhance my skills in this area. Thank you!
Sandy Goodwin of High Impact Coaching & Strategies brought structure and measurable impact to our operations through the invaluable tools and processes he developed. We have successfully designed and implemented a robust Sales & Operations Planning (S&OP) process, significantly enhancing our ability to balance demand and supply across the business. Sandy’s guidance in customer and product segmentation, along with the definition of product families and the implementation of a robust statistical forecasting model, has greatly simplified and improved the accuracy of our demand planning. As an extension of the S&OP process, Sandy established a demand-driven supply chain model design featuring adaptive inventory right-sizing algorithms for finished goods, sub-assemblies, and components that are integrated within Consumption-Based Procurement and Production planning systems. As a result, we have driven a significant improvement in inventory levels while maintaining best-in-class on-time delivery performance. Through the design and implementation of these processes and systems, we transformed a team that had been struggling in the post-COVID era into a high-performing, well-aligned operation.
A new state of the art headquarters facility warrants a world-class manufacturing and service operation. We weren’t looking for an incremental change, we needed step function level change. High Impact Coaching & Strategies offered extensive hands-on experience and a history of results that met our needs…and they delivered.
TheONE DDMRP is an unbelievable tool for managing my inventory. I have been so used to managing excess inventory driven by our forecast. Now we only order based on actual demand requirements rather than based on the forecast or our gut feelings. I used to spend so much time of my day checking items that I had no requirement for, now TheONE DDMRP tells me exactly what is required, significantly reducing excess inventory as well as freeing up my time.
A lot of the positive developments using Demand Flow Technology (DFT) in our manufacturing plant would not have been possible without your support!
High Impact’s consulting services provided a great opportunity for us to understand the concepts of Demand Flow Technology and to implement our new Line Design that generated benefits within our Korean production facility. High Impact provided continual feedback, mentoring, and coaching leading to a detailed understanding and operational benefits that would not have been possible through education alone. They provided an excellent service through all phases of our project that continued beyond their contractual obligations ensuring our continued success. They are a trusted company that we will continue to partner with.
The overall experience was amazing. The material shown was very informative and enlightening. The most important thing that I am taking away from this workshop is the tools needed to become demand driven. I would recommend this class to anyone who wishes to improve production and customer service.
Newsletter Sign Up
Keep up-to-date on what's happening in our Demand Driven World. Get information manufacturing and supply chain topics as well as news on client achievements, up and coming training events and other interesting stuff!
Email
info@highimpactcs.com
Address
High Impact House,
Ashby de la Zouch,
Leicestershire
LE65 1SP. UK
Telephone
US (Toll Free): +1 888 841 8621
UK Telephone: +44 7832 270 381