When manufacturers set out to improve their operations, two proven methodologies often come to the forefront: Lean Manufacturing and Demand Flow Technology (DFT). While both focus on increasing efficiency, reducing waste, and improving flow, they are fundamentally different in how they approach these goals.
Understanding the distinctions between Lean and DFT isn’t just helpful — it’s critical for manufacturing leaders making decisions about how to structure their operations, drive sustainable improvements, and stay competitive in dynamic markets.
In this post, we’ll break down the key differences between DFT and Lean, explore where they align, and explain why these differences matter when selecting the right approach for your organization.
Lean and DFT Share a Common Goal: Flow
Both Lean and Demand Flow Technology (DFT) are designed to achieve flow—the smooth, uninterrupted movement of materials and information from raw materials to finished goods, paced by customer demand.
Many people believe Lean is about waste elimination. That’s partly true. But Taiichi Ohno, the architect of the Toyota Production System, emphasized that the true goal was flow, and that removing waste was simply a means to achieve it.
Ohno also understood that production should be demand driven, tied to actual sales orders rather than forecast-driven production schedules. He eliminated overproduction by developing a pull-based production flow, replacing the traditional forecast-driven scheduling approach. This concept of demand driven production is a fundamental commonality between Lean and DFT.
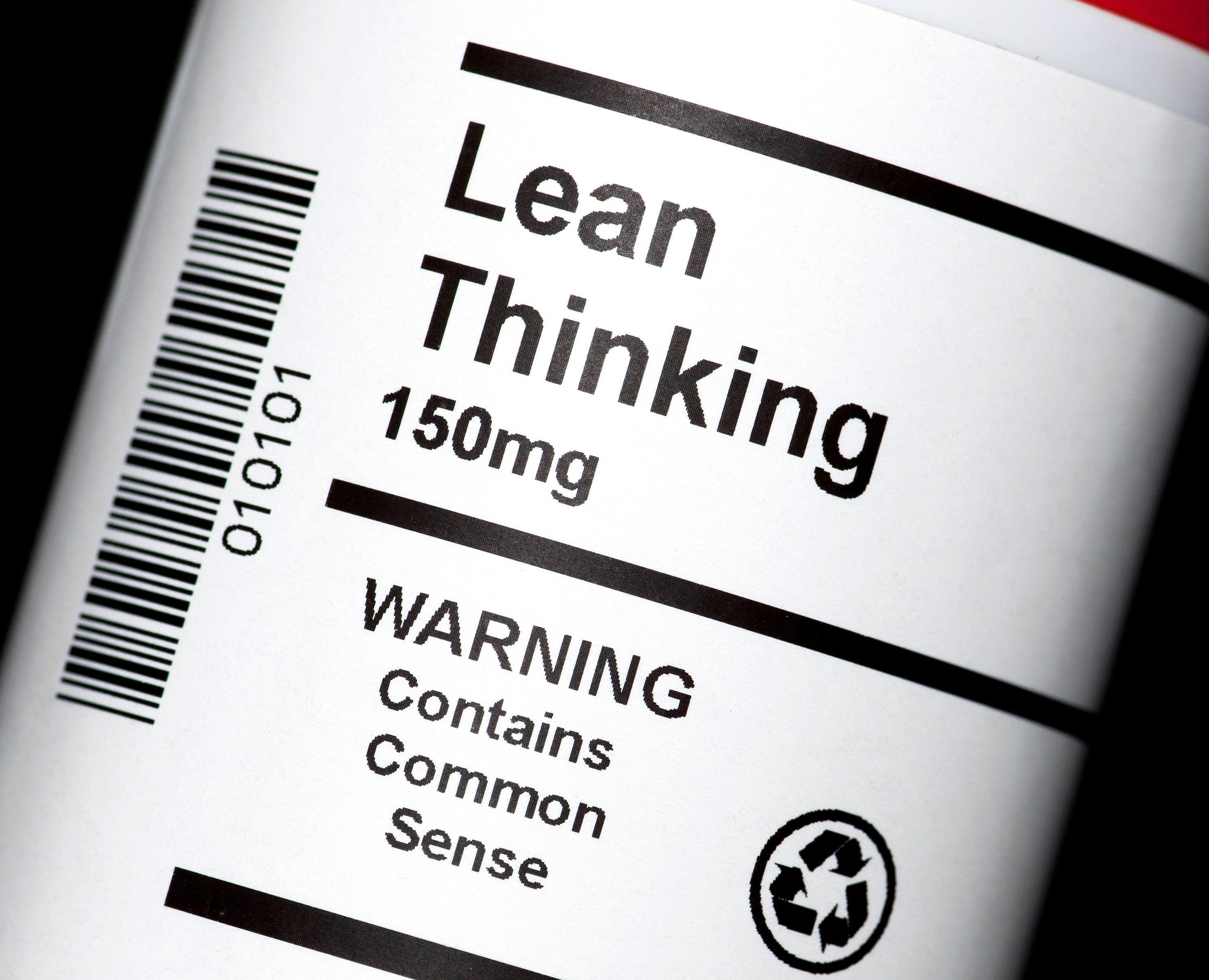
Key Differences: Toolbox vs. Business Strategy
Lean: A Toolbox for Continuous Improvement
Lean provides a set of tactical tools designed for continuous improvement, often deployed one process or area at a time. Common Lean tools include:
- 5S – workplace organization
- SMED – quick changeover
- Kaizen – continuous improvement
- PDCA – Plan-Do-Check-Act problem-solving cycles
- 5 Whys – root cause analysis
These tools are highly effective but typically applied as isolated improvements addressing specific problems rather than as part of a holistic transformation.
Lean encourages a culture of empowerment, where workers at every level can identify and act on opportunities to reduce waste, improve efficiency, and optimize quality. Over time, the compounding effect of these small improvements can be significant.
However, Lean can fall short when the organization lacks a cohesive flow strategy. Improvements are often isolated. One department becomes more efficient, but if upstream or downstream processes don’t change, the benefits are diluted.
The Problem: “Random Acts of Lean”
When Lean is applied without an overarching flow strategy, improvements can become disconnected. CEOs often complain that their Lean investments fail to drive consolidated benefits to the bottom line. Despite significant effort and activity—training, Kaizen events, 5S (or 6sS) blitzes, the financial results are often underwhelming. This is typically because local improvements don’t translate into system-wide gains when processes are not synchronized to demand.
For instance, a successful SMED event may cut setup time in half and double a machine’s available capacity. But if downstream processes aren’t balanced to absorb that capacity, the only result is more WIP piling up between processes—no lead time reduction, no customer benefit. Setup times are lower, the machine is more efficient, but the overall system throughput hasn’t improved. The company just produces inventory faster without moving anything to the customer more quickly.
Or consider a perfectly executed 5S program that organizes a work cell for maximum efficiency. The team works faster and with fewer errors, but if the work cell feeds a process that’s already overloaded, the improved efficiency simply moves the bottleneck further downstream. Instead of solving the real problem, the organization just shifts it.
This is what we call “random acts of Lean”—well-intentioned improvements that lack integration and don’t drive bottom-line results. Because the system isn’t synchronized, local gains are diluted or even negated by mismatches in capacity, sequencing, or demand.
This is where DFT fundamentally changes the game. By designing the entire value stream around actual demand, DFT ensures that every process change contributes to improved flow, shorter lead times, and lower inventory, not just local efficiency improvements but true, system-wide performance gains.
DFT: A Demand Driven Operating Model
Demand Flow Technology (DFT) addresses this issue — not with more tools, but with a unified transformation strategy.
Where Lean often moves area-by-area, DFT looks at the entire production environment and designs flow into the system from the ground up.
It’s a comprehensive manufacturing strategy that redesigns how production is structured, sequenced, and operated based on actual demand. DFT focuses on aligning every process step to customer demand, creating a synchronized and balanced production flow.
This isn’t about shaving seconds off a setup time — it’s about reconfiguring the entire value stream so that products and materials move only as needed, at the rate of consumption, with minimal WIP and short lead times.
This alignment ensures that improvements directly impact lead time, working capital, and customer service.
DFT Is a Step-Change, Not an Iteration
One of the clearest differences is the scale and speed of change. While Lean emphasizes continuous improvement, DFT is a catalyst for rapid transformation that addresses:
- Process balancing
- Takt time alignment
- Flow path design
- Capacity planning
- Mixed-model scheduling
With DFT, the goal is a step-change in business performance — not incremental tweaks, but a comprehensive reorganization of the manufacturing system to flow to demand.
DFT delivers measurable and sustainable performance improvements over a short time frame, including:
- Significant reduction in lead time
- Reduction of WIP inventory
- Improved on-time delivery
- Enhanced responsiveness to demand
- Lower cost of goods sold
Companies that adopt DFT often describe the experience as a paradigm shift. It’s not about adjusting one area at a time — it’s a coordinated redesign of how the entire facility operates.
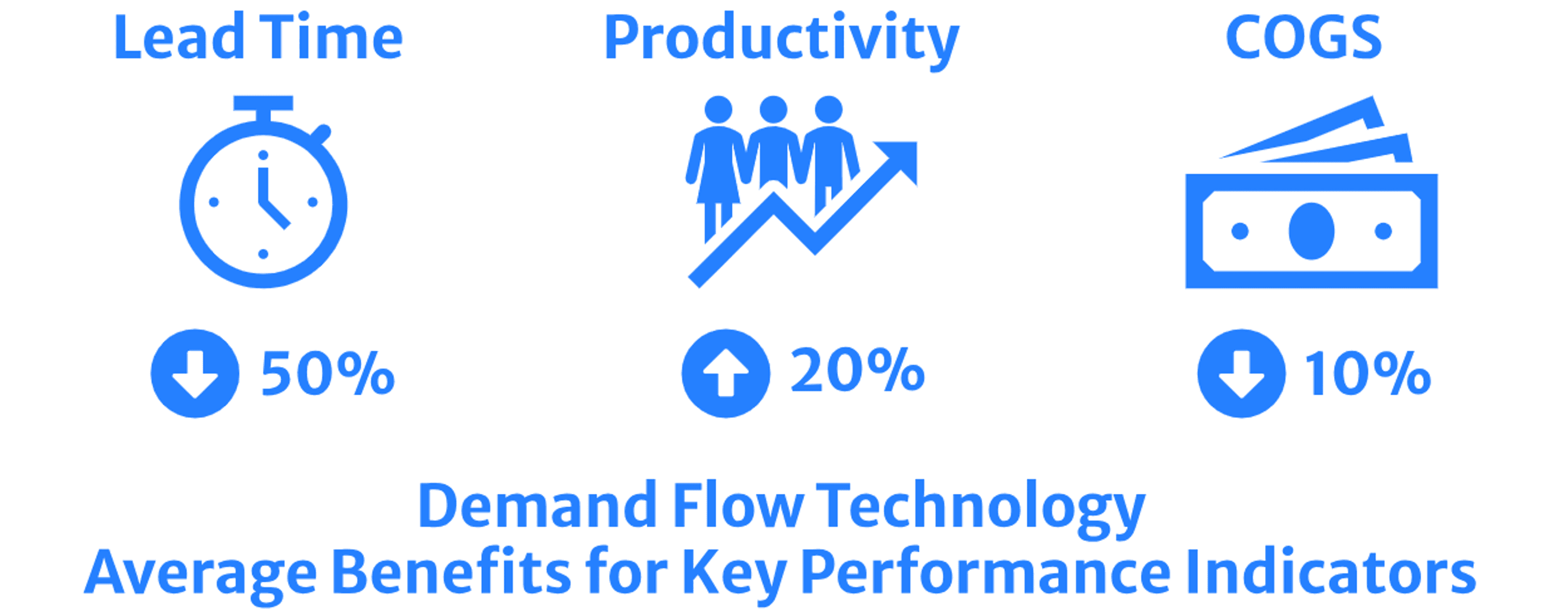
Lean and DFT Are Not Mutually Exclusive
It’s important to recognize that DFT and Lean are not opposing methodologies — they are highly complementary.
DFT creates the structural foundation for flow by designing operations to align directly with demand. It transforms the production environment at a systemic level, addressing flow, balance, and synchronization across the entire value stream.
However, DFT doesn’t discard Lean tools; it fully embraces them. Tools such as 5S, SMED, and Kaizen play an essential role in the DFT transformation process. These tools drive operational improvements that enable and accelerate the adoption of the new flow design.
- 5S ensures that workspaces are organized and standardized to support efficient flow.
- SMED reduces changeover times, making flow lines more flexible and capable of reacting to demand fluctuations.
- Kaizen removes obstacles that could prevent flow from stabilizing.
In this way, Lean tools deliver quick wins that enhance the DFT transformation, while DFT provides the structured flow design that links those wins directly to customer demand. Once implemented, Lean continues to refine and sustain the demand driven flow.
Why the Distinction Matters
If your organization is struggling with siloed Lean efforts that don’t deliver bottom-line results, DFT offers a strategic, system-wide reset.
Both systems share a common objective — but how they achieve it, and when they are best applied, depends on your starting point and your goals.
Understanding the distinction between Lean and DFT is critical because it impacts how organizations approach improvement:
- Lean is highly effective at driving continuous improvement, reducing waste, and improving productivity — often one area at a time. However, without a structured demand driven flow design, Lean improvements can become isolated and fail to convert into company-wide, bottom-line results — “random acts of Lean.”
- DFT, by contrast, builds a fully connected, demand driven operating model. It synchronizes production with customer demand, reducing lead times, inventories, and costs while improving responsiveness.
But DFT is not “set it and forget it.” Once the demand driven flow is established, it must be maintained and periodically redesigned.
As Lean improvements drive further efficiency — reducing cycle times, changeovers, and non-value-added activities — the production system will require fewer resources, lead times will shorten further, and capacity may open up.
At the same time, if the business grows, the product mix shifts, or market conditions change, the original DFT design — while optimized for the current state — has a natural lifespan. As the gap between the original design and current operational realities grows, the DFT flow must be reassessed, refined, and rebalanced to stay aligned with customer needs.
Failing to do so can lead to mismatches between process capacity and demand, eroding the very flow DFT was designed to create. Organizations that treat DFT as a static solution risk slipping back into inefficiency as conditions change.
In essence, DFT creates the foundation, and Lean continuously enhances it — but both must evolve together.
Conclusions
Lean and Demand Flow Technology (DFT) both strive for the same end goal: a production system that flows seamlessly in response to real customer demand. Yet, their approaches are fundamentally distinct and highly complementary.
- Lean offers a toolbox for continuous process improvement. It equips organizations with a powerful set of tools and a culture of continuous improvement, enabling targeted waste reduction and incremental gains across the value stream. However, without a unifying flow strategy, these improvements risk becoming disconnected, limiting their impact on overall business performance.
- DFT delivers a holistic, demand driven design and operating model for the entire manufacturing operation. By redesigning the entire production system to align with actual demand, DFT achieves rapid, systemic transformation, reducing lead times, inventories, and costs while boosting responsiveness and customer satisfaction.
Aspect | Lean | Demand Flow Technology (DFT) |
Purpose | Continuous improvement | Strategic transformation |
Approach | Incremental, tool-based | System-wide, demand driven |
Tools | 5S, SMED, Kaizen, PDCA, etc. | Flow design, demand scheduling, DFT logic |
Scope | Process or department level | Entire production system |
Impact | Localized gains | Step-change in lead time, inventory, cost |
Flow Strategy | Emergent from improvement | Engineered from demand backward |
Sustainment | Core principle | Supported via Lean tools post-DFT. DFT Redesign as company strategies, markets etc. change |
In today’s dynamic manufacturing environment, neither approach is static. While DFT establishes the architecture for flow, ongoing Lean improvements are essential to refine processes, eliminate new forms of waste, and ensure the system stays aligned with evolving business needs.
Once a demand driven flow is established, it must be maintained and periodically refined. As Lean improvements drive greater efficiency or as your business evolves—through growth, shifts in product mix, or changing market conditions—the original DFT flow design may become misaligned with current realities. When this happens, DFT provides the structured approach to reassess, rebalance, and redesign the flow so operations remain tightly synchronized with actual customer demand and business strategy.
Organizations that treat DFT as a static solution risk slipping back into inefficiency and losing their competitive edge. By regularly refreshing the flow design using DFT principles, manufacturers can remain agile and competitive, adapting quickly to new challenges and opportunities in the market.
Ultimately, the choice is not between Lean and DFT, but how to integrate both for maximum impact. By building a demand driven foundation and fostering a culture of continuous improvement, manufacturers can unlock sustainable operational excellence and long-term business success, achieving:
- Faster lead times
- Lower working capital
- Increased flexibility for demand changes
- Sustainable productivity gains
- Stronger competitive advantage
Leveraging the strengths of both—and using DFT to periodically realign flow with business needs—unlocks the full potential of a truly demand driven manufacturing system. Organizations that understand how these methods complement each other can unlock the true potential of both — achieving rapid transformation through DFT and sustaining excellence through Lean.
Demand Driven Supply Chain Solutions
Wherever you manufacture, High Impact Coaching & Strategies can help you to reduce your Cost of Goods Sold by up to 23%, increase productivity by up to 69%, reduce manufacturing lead times by up to 90%, and increase capacity by up to 66%. By ALIGNING manufacturing and the supply chain to customer demand, promoting AGILITY to meet customer demand volatility, and ADAPTING capability as change takes place, we deliver exceptional results for our clients worldwide.
We provide our customers around the world with solutions that create synchronization and balance through the entire supply chain, creating a competitive advantage in their marketplace. Demand Driven Supply Chains drive operational capabilities, generating sustainable bottom-line benefits.
In the factory, Demand Flow Technology focuses on the design and operation of the manufacturing flow. It is a comprehensive mathematical-based methodology that balances resource capability to actual, or planned demand, enabling a company to improve response capability to customer orders, reducing lead time, working capital, and Cost of Goods while improving productivity and overall customer satisfaction. DFT is the framework that enables manufacturing to be adaptive to daily changes in the required mix and actual demand.
Demand Driven Supply Chains focus on the optimization of strategically positioned inventory that absorbs demand volatility and supply variation, we see in the bullwhip, creating stability in supply downstream and demand creation upstream. Dynamic and statistically designed inventory levels based on current market conditions will reduce overall inventory across the entire supply chain while improving customer service levels and response capability. By being able to quickly adapt to changes in customer preferences or market conditions, Demand Driven companies can improve their customer satisfaction and increase their market share.
For further information or to inquire how you can implement Demand Driven Supply Chains please email us at info@highimpactcs.com or send a message via our contact page.
Manufacturing & Supply Chain Information
Previous Insights from High Impact Coaching & Strategies:
- What is Demand Flow Technology
- The Tools of Demand Flow Technology
- How Demand Flow Technology Impacts The Health of Your Business (3-part series)
- Cash Flow Generation is a Priority (2-part series)
- Review of a Recent Demand Flow Technology Implementation
- An Introduction to Sales and Operations Planning S&OP (2-part series)
- What is Supply Chain Management?
- Supply Chain Planning & Engineering
Overview of High Impacts’ Demand Driven strategies that will transform your factories and supply chain network:
LinkedIn Information:
Talk to us today to learn more about how we can help your organization become Demand Driven through the adoption of our Demand Driven methodologies, Demand Flow Technology and Demand Driven Supply Chains.
Newsletter Sign-Up
Keep up-to-date on with what’s happening in our Demand Driven World. Get information manufacturing and supply chain topics as well as news on client achievements, up and coming training events and other interesting stuff!
0 Comments
Leave a comment