The Supply Chain Operations Reference (SCOR) Model was developed in the late 1990s by a consulting firm now part of PricewaterhouseCoopers (PwC) and AMR Research, now part of Gartner. SCOR is a management tool that enables a company to address, improve and communicate supply chain management decisions within the organization and across its supply chain. The SCOR model describes the business processes, internally and externally, that are utilized to satisfy customer demand, therefore, providing a basis for supply chain improvement.
SCOR breaks up the supply chain by looking at key elements or business processes with the supply chain that focus on planning (PLAN), sourcing (SOURCE), manufacture (MAKE), logistics (DELIVER), reverse logistics (RETURN) and supporting (ENABLE). The model integrates re-engineering, benchmarking, and performance measurement into the overall framework to support and improve the effectiveness of supply chain management, communication and improve related supply chain processes.
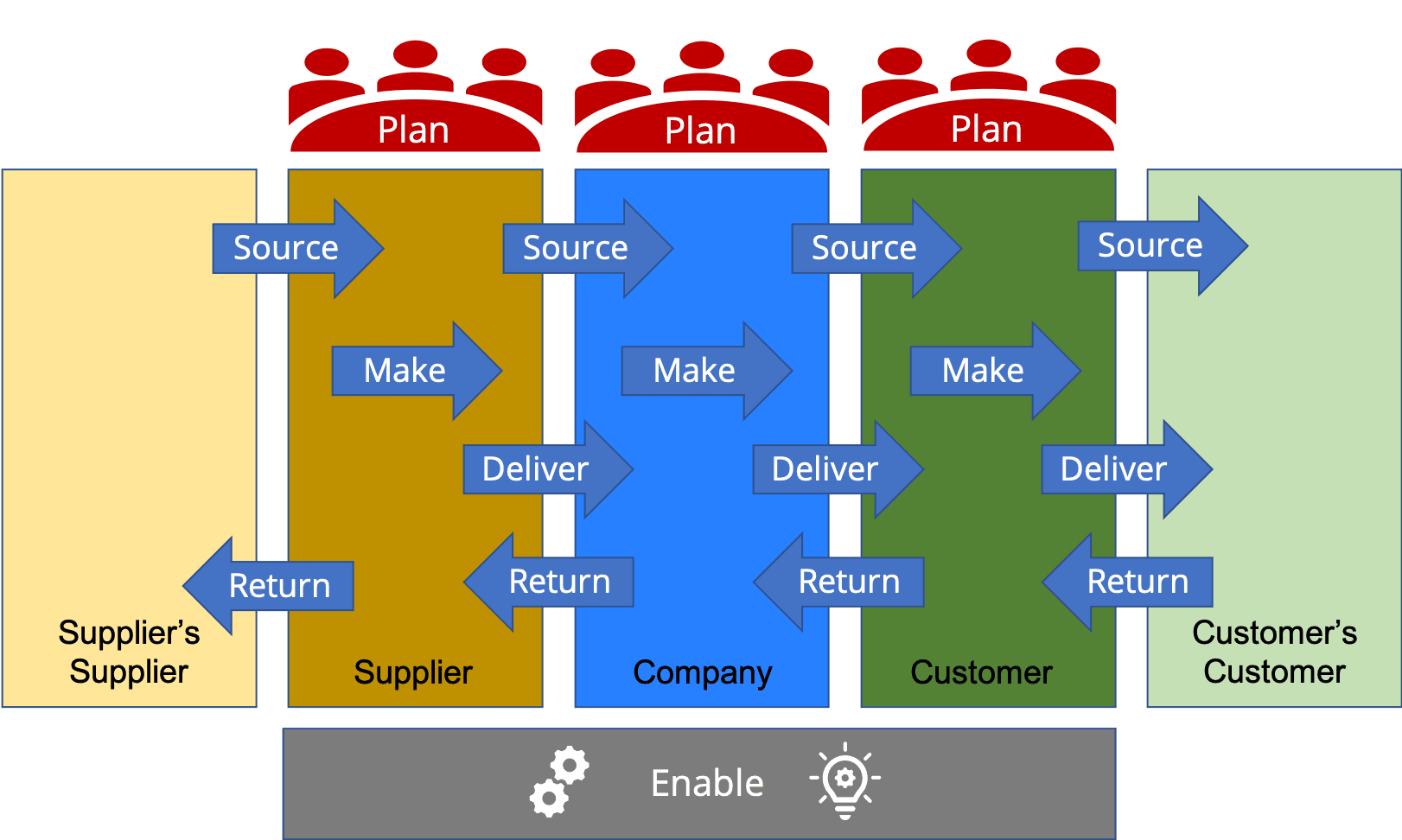
Plan
This first process of the SCOR model describes the activities associated with developing plans to operate the supply chain and is focused on demand and supply planning. Planning is essential to be able to control inventory and manufacturing. Companies have always attempted to match supply to demand developing a course of actions to enable the business to serve the customer base. Both the understanding and management of supply and demand will most likely include the integration of the company within the external supply chain. In planning companies need to monitor demand and supply variation across the supply chain to avoid the bullwhip effect.
At High Impact, one of our demand driven supply chain solutions is Demand Driven MRP (DDMRP) which actively avoids the bullwhip using strategically positioned inventory buffers to absorb the volatility of demand and variation in supply. Companies can become significantly more responsive to their market while dramatically reducing lead time, eliminating variability and volatility across the entire supply chain enabling a company to build an agile and resilient supply chain.
The planning of the supply chain will include planning to source, planning to make, planning to deliver, and planning to return. Elements of planning include balancing requirements and resources to determine capabilities and gaps in demand or resources and identify actions to correct these gaps along the entire chain. The plan also includes the definition of the business rules to develop best practices for supply chain efficiency, through improvement (KAIZEN) and performance measurement. Senior supply chain professionals within the business will develop the business rules to cover inventory, transportation, assets, and regulatory compliance, among others. Ultimately, defined rules will enable the supply chain plan to align with the financial plan of the company.
Source
This covers the identification of the suppliers who will then be used to procure goods or services to meet the planned or actual demand in the most profitable and efficient way. Again, another process where there is direct integration outside of the organization. This process describes the required infrastructure for sourcing and material acquisition to take place. It describes how to manage inventory, supplier agreements, quality levels, and performance.
Make
The next phase of the SCOR model is Make and it focuses on manufacturing and production. Is the manufacturing strategy make-to-order, make-to-stock, or engineer-to-order? This process covers all activities covering the conversion of raw materials and purchased parts into the final product to meet the planned or actual demand. Conversion of materials is used rather than ‘production’ or ‘manufacturing’ as Make represents all types of material conversions such as assembly, chemical processing, maintenance, repair, overhaul, recycling, refurbishment, remanufacturing, and other common names for material conversion processes. Additionally, activities will include, test, paint, packing, material supply, and releasing. It also includes managing the production network, equipment and facilities, and internal transportation.
To ensure that manufacturing meets the needs of the customer it is critical that the manufacturing environment has sufficient resource capacity and is designed to facilitate the flow of product through the organization in the most profitable and efficient way. At High Impact our Demand Driven manufacturing solutions are renowned for transforming organizations around the world, as documented in our case studies. Our focus in the factory is Demand Driven Flow Technology (DDFT) a comprehensive, mathematically-based business improvement strategy designed to drive high levels of response capability, compress lead times, improve productivity and reduce costs enabling manufacturers to become more effective in meeting the needs of their customers. Our successes and client benefits speak for themselves!
Deliver
Deliver is the business process that will provide the finished product to the customer or the distribution center as agreed by the demand plan. This process describes the activities associated with the creation, maintenance, and fulfillment of customer orders. The deliver process will provide a further level of integration across the overall supply chain. Delivery includes order management, warehousing, and management of finished inventories, scheduling order delivery, pick, pack and shipment, and invoicing.
Return
In any business that provides goods, there will be a need for the return of containers, packaging, or defective product. The return process describes the activities associated with the reverse flow of goods and involves the management of business rules, returned inventory, assets, transportation, and post-delivery customer support. The return step will provide a further competitive advantage for a company just as being able to produce and deliver a quality product on time.
With environmental sustainability a major focus for businesses and individuals around the world, the Return processes are key to integrating the reverse supply chain. In addition to the historical return of defective products, companies need to consider environmental regulatory requirements that may require them to recycle products when they reach their end of life. In addition, companies for many years have worked with their customers to minimize packaging waste creating returnable containers/packaging that can be reused. A prime example of this are Kanban containers that cycle between supplier and customer as part of any Lean or DDFT material replenishment system.
Enable
The final phase of SCOR is the Enable processes that are associated with the management of the supply chain to support the overall framework and the improvement of the supply chain. Enable processes include the management of business rules, performance management, data management, resource management, facilities management, contract management, supply chain network management, managing regulatory compliance, and risk management.
Benefits of Using the Supply Chain Operations Reference (SCOR) Model
The SCOR process helps companies to analyze their supply chain at many levels to identify the current state of their supply chain. Each of the five initial steps repeat over and over again across customers and suppliers linking them to the organization. The analysis of each step of the SCOR model helps an organization to measure the overall performance of its supply chain to identify the inefficiencies, problems and gaps. The model enables full leverage of capital investment, creation of a supply chain road map, alignment of business functions, and an average of two to six times return on investment.
Demand Driven Supply Chain
Some companies go down the route of stocking huge amounts of inventory only to find they stocked the wrong inventory. Some will create excess capacity with the manufacturing plant so they can ramp up quickly as demand ramps up but machines sit idle. The design of the supply chain needs to be Demand Driven and based on the business model and rules, to enable the reduction/elimination of excess inventory costs, and the positioning of optimum resource capacity. A Demand Driven supply chain model will give you just that where we integrate our Demand Driven solutions of Demand Driven Flow Technology (DDFT) with Demand Driven MRP (DDMRP).
A Demand Driven Supply Chain from High Impact Coaching & Strategies will enable responsive, agile manufacturing, and end to end supply chain optimization that will reduce your costs, inventory and lead times transforming your business into a world-class Demand Driven organization at the forefront of your industry.
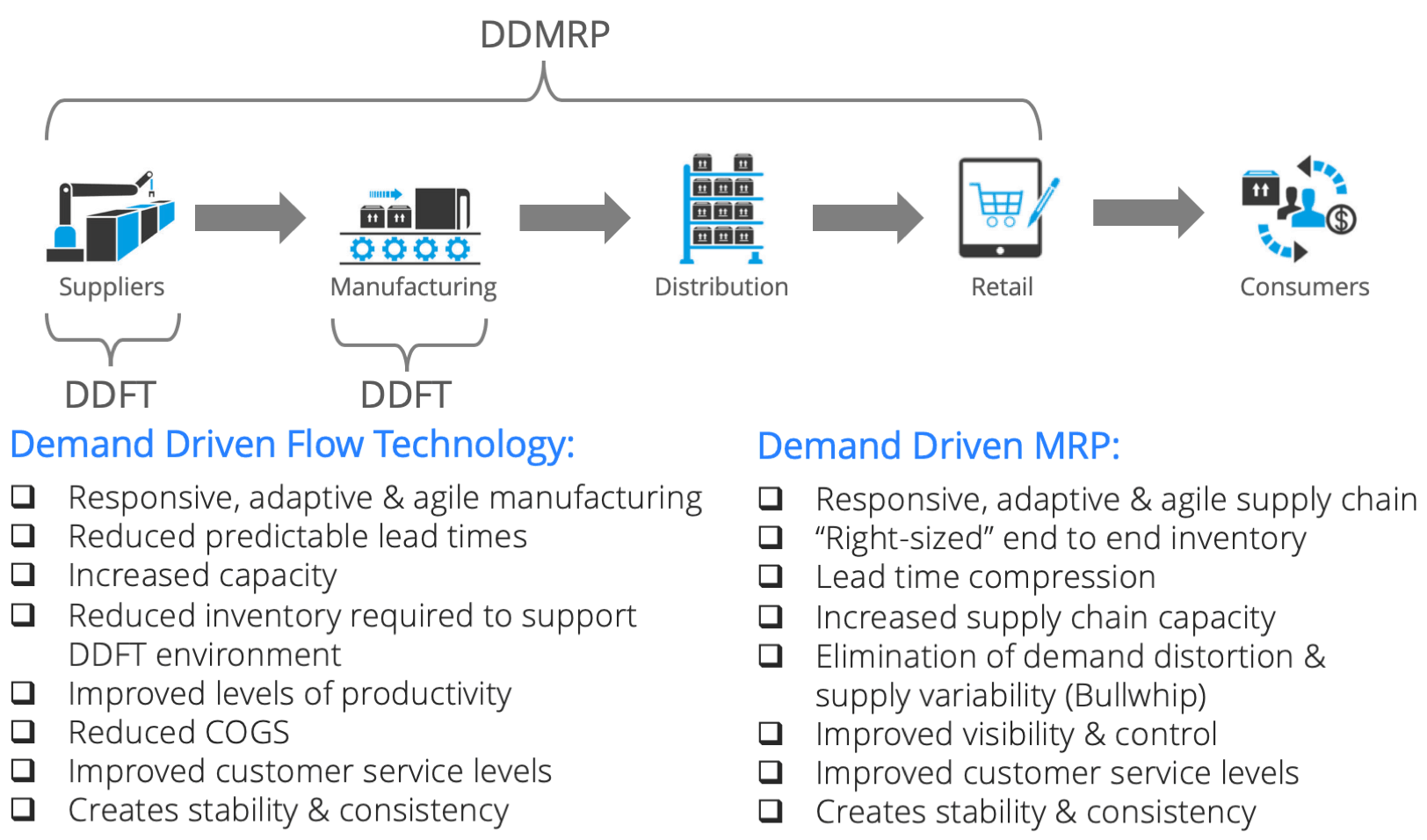
Demand Driven Supply Chain Management Solutions
We provide our customers around the world with solutions that create synchronization and balance through the entire supply chain creating a competitive advantage in their marketplace. Demand Driven supply chains drive operational capabilities generating sustainable bottom-line benefits.
In the factory, Demand Driven Flow Technology focuses on the design and operation of the manufacturing flow. It is a comprehensive mathematical-based methodology that balances resource capability to actual, or planned demand, enabling a company to improve response capability to customer orders, reducing lead time, working capital, and Cost of Goods while improving productivity and overall customer satisfaction. DDFT is the framework that enabling manufacturing to be adaptive to daily changes in the required mix and actual demand.
Demand Driven MRP is the planning engine that drives the supply chain and the factory. It focuses on the optimization of strategically positioned inventory along the supply chain that absorbs demand volatility and supply variation we see in the bullwhip creating stability in supply downstream and demand creation upstream. Mathematical buffer designs that dynamically optimize inventory levels based on current market conditions and will reduce overall inventory across the entire supply chain while improving customer service levels and response capability. DDMRP provides the Supply Chain Planning and Execution tools to enable a company to become Demand Driven so that it can meet the expectations of its customers in today’s complex and volatile marketplace.
DDFT and DDMRP work together using actual demand to drive the Demand Driven supply chain removing traditional reliance on forecasting to drive the supply chain. The Demand Driven Supply Chain management activities still use the forecast, but now as an input for the Demand Driven Sales & Operations Planning (DDS&OP) process. DDS&OP will adapt the supply chain model based on the various business conditions and the forecast appropriately resizing the inventory buffers. Supply orders are now generated based on actual consumption from the dynamic buffers rather than based on a forecast requirement.
For further information or to inquire how you can implement Demand Driven Supply Chains please email us at info@highimpactcs.com or send a message via our contact page.
Talk to us today to learn more about how we can help your organization become Demand Driven through the adoption of our Demand Driven methodologies, DDMRP and Demand Driven Flow Technology.
Newsletter Sign-Up
Keep up-to-date on with what’s happening in our Demand Driven World. Get information manufacturing and supply chain topics as well as news on client achievements, up and coming training events and other interesting stuff!