Total Cost of Ownership, geopolitical instability, extreme weather conditions, and post-pandemic supply chain disruptions are some of the key considerations that are impacting supply chain strategy and driving offshoring & reshoring decisions for many companies.
In this two-part post, we are going to explore why Offshoring became popular and why for some companies reshoring or diversifying the supply chain is now a key business strategy.
In Part 1 we focused on why companies moved their production and supply chains offshore and what started companies in 2007 to start thinking about reshoring. Now we will discuss the recent rise in the reshoring movement and the factors and events driving executive decisions today.
Is the Reshoring Movement Starting to Gain Momentum Again?
Several factors have contributed to the recent rise in the reshoring movement. The cost of shipping goods across borders has skyrocketed in recent years due to multiple factors, such as the rising cost of fuel and congestion in ports and shipping lanes. As a result, companies are finding it more expensive to offshore their operations and are looking for ways to improve the reliability of their supply chain.
The COVID-19 pandemic and recent geopolitical tensions have introduced new obstacles for companies to navigate. With these challenges in mind, many businesses are taking a fresh look at their offshore production strategies. Some are considering reshoring or diversifying their supply chains to mitigate the risks associated with geopolitical instability.
Following the significant slump in global demand during the pandemic, the subsequent worldwide start-up led to disrupted global supply chains and significantly increased lead times. As a result, there have been worldwide shortages of critical components and materials throughout most of 2022, and in 2023 lead times are still longer than average. This has highlighted the risks associated with relying on a single offshore location for production. According to a recent report by Everstream Analytics, China’s rapidly changing COVID-19 policies have created ongoing challenges for manufacturers as they struggled to adapt to shifting local policies.
Both the pandemic and the post-pandemic period have exposed the risks associated with relying on a single offshore location for production. According to a 2023 report by Everstream Analytics, “China’s rapidly changing COVID-19 policies have created ongoing headaches for manufacturers as companies and workers struggle to adapt to shifting local policies”.
Additionally, the report found that sourcing from China also poses financial risks. When compared to the US and Germany, China accounted for the highest share of insolvencies in the electronics, automotive, and chemical sectors. The risk of financial insolvencies disrupting supply chains in the future is also a concern with potential downturns in demand and cutbacks in purchasing. The report suggests that a single supplier business bankruptcy would lead to a bullwhip effect that could halt production as well as adding costs and time while alternative options are sought.
Recent geopolitical tensions between countries such as the US and China have created new uncertainties regarding trade policies and regulations. Furthermore, a key tension that has impacted the decision-making process for offshoring and reshoring is the relationship between China and Taiwan. The two countries have a complex history, with China claiming Taiwan as a part of its territory, while Taiwan considers itself an independent state. This has led to tensions between China and other countries that have close ties to Taiwan, including the United States, Japan, and many European nations.
Geopolitical tensions are also highlighted in the Everstream report, identifying “177 sub-tier suppliers linked to forced labor of the Uyghur people in China’s Xinjiang region”. US Congress has also been questioning automotive manufacturers and the fast fashion company, Shein, about their processes to ensure forced labor in Xinjiang is kept out of their supply chains.
As geopolitical tensions continue to rise, companies that rely on offshore production in China or other countries in the region are facing significant uncertainty and risk. Organizations are now having to consider what disruptions in their supply chains they could face due to the possibility of geopolitical events, such as trade disputes, sanctions, or even military conflict. Moreover, companies can face reputational risks if they are perceived as supporting policies or actions that are seen as threatening the security or stability of the region. This has made it difficult for companies to plan and make long-term investments in offshore production.
Climate change and recent extreme weather conditions are also shaping global supply chains. Countries such as China, the US, and India are being impacted by severe droughts, flooding, and wildfires, leading to disruptions in production and transportation. Companies are increasingly taking steps to mitigate these risks by diversifying their supply chains, investing in sustainable practices, and exploring new technologies. Climate change is likely to continue to impact supply chains in the future.
Governmental Subsidies and Incentives
Recent US government subsidies within the semiconductor and green energy sectors have also incentivized some companies to reshore production back to the US. The subsidies aim to increase domestic production capacity and reduce dependence on foreign sources. By providing financial support to these industries, the US government is encouraging companies, to invest in domestic production and create jobs.
These incentives came at the right time. If supply chains were running smoothly, there would be little pressure to build new semiconductor factories outside of South East Asia. The aforementioned post-pandemic supply chain disruptions and geopolitical instability are driving the growth of semiconductor construction spending in the US. Planned US-based semiconductor projects are expected to require an investment of $223 billion to $260 billion through 2030. A recent article in the Wall Street Journal also highlights that manufacturing construction spending in the US had reached a record $108 billion in 2022, higher than what was being spent on education, healthcare, and offices.
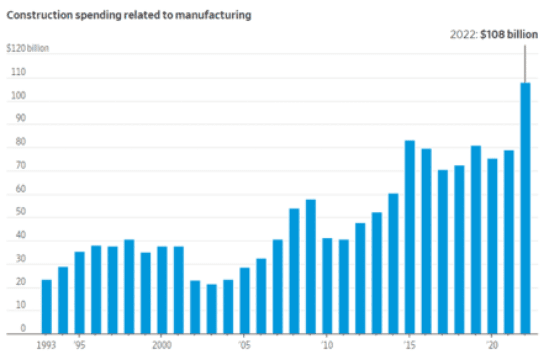
Source: Supply Chain Digest, 21st April 2023. A Look at the State of US Manufacturing
US subsidies are certainly attracting domestic and foreign investment from the semiconductor industry. It is also the case with other industries. BBC News interviewed John Neil the Executive Chairman of UK-based Unipart Group, an automotive parts manufacturer and logistics company. Mr Neil discussed that the UK was going to have difficulty competing with the US, who “are redefining the free enterprise system”. Even Unipart a proud UK company is now considering investment in the US versus the UK due to the subsidies being offered.
America’s Inflation Reduction Act (IRA), passed last year, was offering firms a “completely game changing set of incentives and fiscal support” that was hard to ignore
I’ve asked our team to think very carefully about our investment strategy in the US and our US operations and whether we should be pivoting more into those markets
Conclusions
As global uncertainties continue to challenge the supply chain industry, companies are exploring new ways to mitigate risks and ensure resilience. Some are increasingly considering reshoring production back to their home countries or diversifying their supply chains. This approach not only reduces the exposure to single offshore locations but also provides greater control and flexibility within the supply chain. Moreover, reshoring can help businesses reduce the impact of tariffs and other trade-related risks.
When considering the Total Cost of Ownership, it often makes more sense for companies to produce or source products domestically, even if labor costs are higher. This is because shorter lead times and lower inventory holdings make up for the increased labor costs. Producing locally will also improve responsiveness and flexibility, which is one of the reasons why Lego is relocating from Mexico to invest in a new US plant in Virginia. By being closer to the market, companies can better cater to customer needs and adapt to changing market demands.
Offshoring or reshoring production is a critical decision that requires a thorough evaluation of various factors, such as labor costs, skilled workforce, technology, market access, and Total Cost of Ownership. In the past, offshoring to China was considered a cost-cutting strategy for many organizations, but with the COVID-19 pandemic, ongoing supply chain disruptions, geopolitical tensions and recent high-impact weather conditions, this approach has become increasingly uncertain. As a result, businesses are now taking a more cautious approach and weighing the risks and benefits of offshoring and reshoring to make informed decisions about production location.
The reshoring movement is still in its early stages, but it is gaining momentum. The factors behind this movement are here to stay, which means we can anticipate an increase in manufacturing companies bringing their operations back to their home country. The Reshoring Institute found that the number of manufacturing jobs in the United States increased by 75,000 in 2021. This was the first year since 2010 that manufacturing jobs had increased in the United States. In cases where reshoring costs remain prohibitively high, we can also expect to see a rise in supply chain diversification.
Reshoring and diversifying supply chains are great ways to reduce supply chain risks, improve control, and increase flexibility. As we move towards a post-pandemic world, it is important for businesses to re-evaluate their supply chain strategies and ensure they are well-equipped to handle any future disruptions. By doing so, they can develop a resilient and sustainable supply chain strategy that aligns with their business objectives and priorities.
Demand Driven Supply Chain Solutions
Wherever you manufacture, High Impact Coaching & Strategies can help you to reduce your Cost of Goods Sold by up to 23%, increase productivity by up to 69%, reduce manufacturing lead times by up to 90%, and increase capacity by up to 66%. By ALIGNING manufacturing and the supply chain to customer demand, promoting AGILITY to meet customer demand volatility, and ADAPTING capability as change takes place, we deliver exceptional results for our clients worldwide.
We provide our customers around the world with solutions that create synchronization and balance through the entire supply chain creating a competitive advantage in their marketplace. Demand Driven supply chains drive operational capabilities generating sustainable bottom-line benefits.
In the factory, Demand Flow Technology focuses on the design and operation of the manufacturing flow. It is a comprehensive mathematical-based methodology that balances resource capability to actual, or planned demand, enabling a company to improve response capability to customer orders, reducing lead time, working capital, and Cost of Goods while improving productivity and overall customer satisfaction. DFT is the framework that enables manufacturing to be adaptive to daily changes in the required mix and actual demand.
Demand Driven supply chains focus on the optimization of strategically positioned inventory that absorbs demand volatility and supply variation we see in the bullwhip creating stability in supply downstream and demand creation upstream. Dynamic and statistically designed inventory levels based on current market conditions and will reduce overall inventory across the entire supply chain while improving customer service levels and response capability. By being able to quickly adapt to changes in customer preferences or market conditions, Demand Driven companies can improve their customer satisfaction and increase their market share.
For further information or to inquire how you can implement Demand Driven Supply Chains please email us at info@highimpactcs.com or send a message via our contact page.
Manufacturing & Supply Chain Information
Previous Insights from High Impact Coaching & Strategies:
- What is Demand Flow Technology
- What Is The Difference Between Lean and Demand Flow Technology?
- The Tools of Demand Flow Technology
- How Demand Flow Technology Impacts The Health of Your Business (1st of 3 Parts)
- Cash Flow Generation is a Priority (1st of 2 Parts)
- Review of a Recent Demand Flow Technology Implementation
- An Introduction to Sales and Operations Planning S&OP (1st of 2 Parts)
- What is Supply Chain Management?
- Supply Chain Planning & Engineering
- The Supply Chain Methodology That is DDMRP
- What is DDMRP?
- MRP – Solution or Problem
- A Solution to Excess Inventories, Stocks-Outs & Poor Customer Service?
- Adapt or Die – Become Demand Driven
- Supply Chain Brain: DDMRP as an Emerging Disruptive Supply Chain Capability
- What Does VUCA Mean?
Overview of High Impacts’ Demand Driven strategies that will transform your factories and supply chain network:
LinkedIn Information:
Talk to us today to learn more about how we can help your organization become Demand Driven through the adoption of our Demand Driven methodologies, DDMRP and Demand Flow Technology.
Newsletter Sign-Up
Keep up-to-date on with what’s happening in our Demand Driven World. Get information manufacturing and supply chain topics as well as news on client achievements, up and coming training events and other interesting stuff!